何飞
川南煤业有限责任公司鲁班山北矿,四川 筠连 645250
摘要:煤与瓦斯突出矿井综采工作面初采期间当采空区悬顶面积过大瞬间垮落时极易形成飓风、冲击压而造成人员伤亡和设备损坏,且极易造成瞬间大量瓦斯涌出,诱发重特大瓦斯事故。鲁班山北矿通过采用深孔预裂爆破方法对综采工作面进行深孔预裂爆破强制放顶,缩短了综采工作面初次来压步距,减少采空区悬顶面积,架后矸石充填率达到了预期,保证了安全生产。
关键词:煤与瓦斯突出矿井;深孔预裂爆破;强制放顶
0 前言
综采工作面采空区顶板大面积来压主要是坚硬顶板被采空的面积超过一定极限值、发生大面积垮落而造成剧烈的动压现象。目前综采工作面一般采取自然垮落法处理采空区,对于厚硬砂岩顶板,若不采取强制放顶措施,随着工作面的推进,悬顶面积日益增大,当悬顶面积超过一定极限值时,极易在采空区积聚大量瓦斯,会发生顶板大面积来压,造成支架压死,其大面积垮落形成的飓风,还会对工作面人员作业安全产生威胁;鲁班山北矿属煤与瓦斯突出矿井,综采工作面顶板大面积来压会使瓦斯突然大量的涌出,诱发瓦斯事故。综采工作面深孔预裂爆破强制放顶不仅可以消除顶板大面积来压,减小来压强度和来压步距,减少采空区瓦斯积聚,避免大范围性的瓦斯涌出、支架损坏及飓风威胁,冒落的矸石能够减少老塘有害气体积存,还能对上覆岩层起到支撑作用,优化工作面巷道的围岩应力环境,减轻巷道受压变形,便于巷道维护。
1 工作面概况
1418综采工作面为鲁班山北矿一水平14采区首采面,该区域7#、8#煤层分岔,根据地质钻孔和周边采掘工作面揭露情况,7#、8#煤层间距为7.8~10.4m,该工作面回采8#煤层,其走向长度为463~467m,平均465m,倾斜长度为135m,工作面煤层倾角为16°~22°,平均18°,开采面积为62775m2。工作面煤层厚度为1.8-4.19m,平均厚度为3.2m,采用走向长壁后退式综合机械化采煤法,一次采全高,初采采取强制放顶,后期采用全部垮落法管理采空区。
工作面采用MG500/1130-QWD型双滚筒采煤机落煤,ZY4000/18/41型掩护式液压支架支护顶板,SGZ830/400型刮板运输机运煤。
1.1 煤层顶底板情况
工作面煤层直接顶为细砂岩、砂质泥岩,老顶为粉砂岩、粗砂岩,详见表1。
表1 煤层顶底板情况表
顶底板
名称 岩石名称 厚 度(m) 岩 性 特 征 描 述
老 顶 粉砂岩、粗砂岩 6.0~8.0m 灰白色中厚层-薄层状粉砂岩、细砂岩夹砂质泥岩
直 接 顶 细(粗)砂岩、砂质泥岩 2.0~4.0m 灰褐色细(粗)粉砂岩、砂质泥岩互层
伪 顶 泥岩、砂质泥岩 0.1~0.30m 浅褐灰色粘土岩、泥岩
直 接 底 粘土岩、泥岩、砂质泥岩 0.8~2.0m 浅灰色泥岩、粘土岩、砂质泥岩互层夹9#煤线
老 底 粘土岩、细砂岩 4.0~7.0m 以浅灰-灰色粘土岩、细砂岩为主
1.2 工作面巷道布置方式
1418工作面机巷、风巷及开切眼布置方式:机巷、风巷、切眼均沿8#煤层顶板以中线施工,其中机巷、风巷沿8#煤层走向布置,切眼沿8#煤层倾向布置,如图1所示。
.png)
2 深孔预裂爆破优先性分析
本工作面煤层直接顶为砂岩,厚度一般为3.0 m左右,岩层致密、坚硬,吸水率较低,注水软化周期长,且高压注水弱化顶板方案在南方矿井应用尚不普及,技术尚不成熟,故综合煤层赋存条件与矿井技术条件,选择深孔预裂爆破方法对工作面顶板进行弱化处理。
3 深孔预裂爆破方案
综合考虑工作面煤层顶板岩性、赋存特点和工作面开采条件,在工作面推进3m后采用深孔预裂爆破在砂帮侧、煤帮侧进行强制放顶。
3.1 爆破参数设计
(1)钻孔倾角α、β
钻孔倾角α是指在 中线剖面图中,钻孔与水平方向的夹角;钻孔倾角β是指在巷道断面图中,钻孔与竖直方向的夹角。倾角的大小,决定了爆破范围和爆破效果,倾角过大,爆破范围缩小,炮眼数目相应增多,工程量增大;倾角过小,爆破后,顶板破碎,不利于安全生产。综合考虑钻机施工、装药、切缝效果、经济性等因素,结合1418工作面实际情况及工程实践经验,确定钻孔倾角α=60°、β=90°。
(2)切顶高度H切
根据岩层破断规律和理论研究分析,位于煤层上方的基本顶是影响工作面顶板垮落的关键岩层,结合1418综采工作面综合地层情况,该工作面基本顶厚度h=4.3m,因此切顶高度H切=h=4.3m。
(3)炮眼深度L
钻孔深度L=H切÷(sinα×sinβ)+0.1
式中:H切—1418综采工作面直接顶上边界高度,H切=4.3m;
α—巷道中线剖面图中,钻孔与水平方向的夹角,α=60°;
β—巷道断面图中,钻孔与竖直方向的夹角,β=90°;
0.1—钻孔穿透基本顶厚度,取 0.1m。
经上式计算,预裂爆破炮眼深度 L=5.07m,施工时取5.0m。
(4)炮眼位置
根据以往综采工作面采空区上、下出口段来压周期较长且垮落效果不好的情况,确定在1418工作面砂帮侧上、下出口各10m均布置双排炮眼;结合钻机施工操作可行性及现场推进等实际情况,砂帮侧第一排炮眼与砂帮的距离确定为1m,砂帮侧上、下各10m第二排炮眼距砂帮为2m;煤帮侧炮眼距煤帮距离为0.3m,要求现场施工时须保证钻孔沿工作面倾斜方向在一条直线上。
(5)炮眼间距D
结合1418综采工作面顶板岩性及坚硬顶板预裂爆破技术要求,初步确定钻孔间距D=1500mm。
(6)单个炮眼装药量
结合1418综采工作面顶板岩性及坚硬顶板预裂爆破技术要求,初步确定单个炮眼装药量为800g。
3.2 强制放顶施工方案
结合上述方面,最终确认施工方案,即在液压支架后方距离砂帮1m位置施工一排炮眼、且在砂帮侧沿工作面倾斜方向的上下端各10米再布置一排炮眼(与砂帮相距2m),距离煤帮0.3m位置施工一排炮眼,其炮眼间距均为1.5m,炮眼角度为60°,每眼装药量为800g,砂帮炮眼深度与煤帮炮眼深度均为5.0m,如下图2所示。
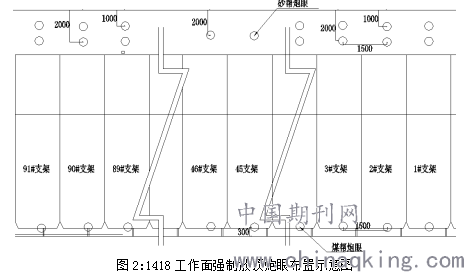
4 强制放顶后现场观测写实情况
由于该工作面机巷进行沿空留巷,前期推进较慢。
工作面推进约7m,现场出现顶板垮冒声,采空区顶板开始出现垮落,通过上下端头及支架间隙观察,采空区下端处顶板垮落严实,工作面中部支架后方垮落矸石充填高度约为0.6m。
工作面推进约15m时,采空区开始初次来压,采空区顶板开始大范围的垮冒,伴有巨大的垮落声,通过支架间隙,可见矸石充填高度已经超过支架架高,采空区上下两端,矸石已经垮下并充填了采空区。
随着工作面的继续推进,采空区顶板基本随采随垮。
5 结论
(1)结合工作面地质条件,制定合理技术参数,采用深孔预裂爆破对工作面进行强制放顶后,通过后期写实观测,工作面在推进15m左右,初次来压开始,减小了来压步距和来压强度,缩小了坚硬砂岩顶板的悬顶面积,避免了顶板大面积来压及瓦斯大量的积聚并涌出所带来的安全威胁。
(2)通过深孔预裂爆破强制放顶后,采空区矸石充填达到预期目的,在工作面推进15m后,采空区矸石能够很好的垮落并充填采空区,对上覆岩层垮落起到了缓冲作用,并减少了通过支架间隙向采空区的漏风量,有利于工作面防灭火管理。
(3)通过深孔预裂爆破强制放顶后,矿压显现不明显,地应力变化逐渐趋于稳定,减轻了工作面顺槽巷道受压变形,有利于巷道维护。
参考文献:
[1]乔轻炳,张宝香.首采工作面初采强制放顶方案设计及应用[J].能源与环保,2017,39(05):121-126.
[2]钱鸣高,石平五.矿山压力与岩层控制[M].徐州: 中国矿业大学出版社,2003.
[3]张冬华,田灵涛.深孔预裂爆破技术在深井坚硬完整顶板强制放顶中的应用[J].煤炭工程,2018,50(01):42-44.
[4]杨相海,张杰,余学义.强制放顶爆破参数研究[J].西安科技大学学报,2010,30( 3) : 287- 290.
[5]高魁,刘泽功,刘建.深孔爆破在深井坚硬复合顶板沿空留巷强制放顶中的应用[J].岩石力学与工程学报,2013,32( 8) : 1588-1594.